Isothermal forging Hydraulic Press
Key Features
Isothermal Superplastic Forming: The Isothermal Hydraulic Press employs an isothermal superplastic forming technique that ensures the precise control of temperature and deformation. This results in a low-stress environment for the material, promoting enhanced plasticity, reduced strain rates, and simplified manufacturing processes.
Efficient and Controlled Forgeability: With its ability to achieve precise control of forging speed and displacement, the press offers exceptional accuracy and repeatability. This ensures consistent and reliable production by eliminating variations and defects commonly seen in traditional forging methods.
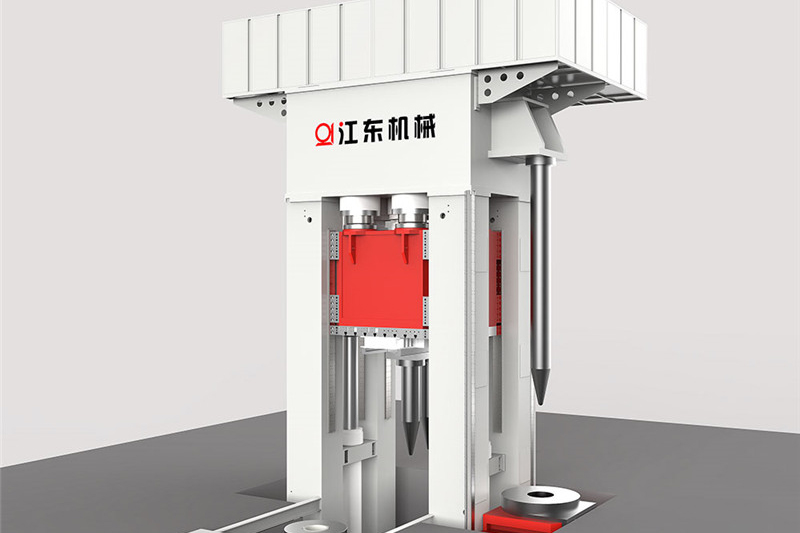
Enhanced Material Plasticity: By reducing the metal's flow resistance and increasing its plasticity, the isothermal superplastic forming process significantly enhances the material's formability. This allows for the production of complex shapes and intricate designs that would be challenging or impossible to achieve using conventional forging techniques.
High-Quality Finished Components: The Isothermal Hydraulic Press ensures the production of high-quality forged components with excellent dimensional accuracy, surface finish, and microstructural integrity. This reduces the need for secondary machining operations, resulting in cost savings and shorter production cycles.
Wide Application Range: The press finds extensive applications in industries such as aerospace, aviation, military, defense, and other fields where the production of intricately shaped, high-strength forged components is critical. It is particularly suitable for manufacturing components used in aircraft structures, engine parts, missiles, defense systems, and high-speed rail.
Improved Efficiency and Productivity: The precise control offered by the press enhances production efficiency and productivity. With reduced lead times, manufacturers can meet demanding production schedules and deliver high-quality components to their customers.
Advanced Control System: Equipped with an advanced control system, the Isothermal Hydraulic Press provides seamless integration of process parameters, including temperature, pressure, and deformation. This allows for precise control, monitoring, and adjustment, ensuring optimal forming conditions and reducing the risk of material defects.
Applications
Aerospace and Aviation Manufacturing: The Isothermal Hydraulic Press plays a crucial role in the aerospace and aviation industries, enabling the production of complex and lightweight forged components. These include aircraft structural elements, engine parts, landing gear, and other critical components that require high strength, dimensional accuracy, and structural integrity.
Military and Defense Industries: In the military and defense sectors, the press is used for manufacturing components required for missiles, military aircraft, defense systems, and naval vessels. The ability to produce intricate shapes and high-strength forged components ensures reliable and robust performance in critical defense applications.
High-Speed Rail Industry: The Isothermal Hydraulic Press finds application in the high-speed rail industry for the production of forging components used in bogies, underframes, and other critical structural elements. The precision and efficiency of the press contribute to the safety and performance of high-speed rail systems.
General Industrial Applications: The press also caters to a wide range of industrial sectors, including energy, oil and gas, and automotive, where high-performance forged components with complex shapes and superior strength are required. It supports the production of customized parts for various industrial applications.
In conclusion, the Isothermal Hydraulic Press is a technologically advanced machine that enables the isothermal superplastic forming of difficult-to-form materials. With its precise control, enhanced plasticity, and wide application range, it significantly improves production efficiency, reduces lead times, and ensures the manufacturing of high-quality forged components. From aerospace and defense to high-speed rail and general industrial applications, the press revolutionizes the forging process, meeting the demands of diverse industries while delivering superior performance and reliability.